Customer Stories: Furukawa Electric Co., Ltd.
Furukawa Electric Co., Ltd.

Using i-Reporter on the production line led to realizing cost reduction in management, achieving faster search speed, and improving analysis efficiency.
Furukawa Electric Co., Ltd. (hereafter, Furukawa Electric) is a non-ferrous metal manufacturer that produces optical fiber, electric cables, wire harnesses, etc.
Since 1884, they have used their materials and technical capabilities cultivated in the copper and electric cable industry to develop unique products.
Furukawa Electric looks beyond the present to develop technology that will contribute to building social infrastructure.

“Previously, we used paper to log and store all our quality records and entered the data into Excel to analyze them. With i-Reporter, our business became more efficient as we digitized records from when they were logged.
Especially when there was a problem in the quality, I noticed that finding the previous quality records and detecting/analyzing the cause has become faster than before. Faster recording and tabulation is also a great value, which allows us to spend more time visualizing and analyzing the production data.” – Mr. Matsumoto.
Contributing to the expansion of Japanese and worldwide infrastructure.
Furukawa Electric continues to develop new technology.
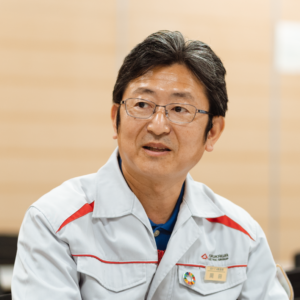
“We will contribute to realizing a truly affluent and sustainable society through continuous technological innovation on top of our material strength cultivated over a century.
Based on this philosophy, Furukawa Electric develops various proprietary products and operates in 6 wide-ranging businesses – from telecommunication like optical fiber, energy infrastructure and electricity, etc.” – Mr. Okada.
In the 1960s, Furukawa Electric expanded overseas, starting with Southeast Asia, including Bangkok, Thailand. Now, the company has built manufacturing plants as far away as Brazil and is creating new technologies and products worldwide. The company has also worked on large transmission electric cable construction projects in Iran from 1978 to 1982 and contributed to developing infrastructure in Japan and worldwide with technology.
The optical fiber business, in which Furukawa Electric has recently started using i-Reporter for manufacturing process management, is another technology that they have been working on. While still in its pioneering years in 1974, Furukawa Electric has a history of successfully field-testing the world’s first optical fiber cable.
Currently, the company has manufacturing facilities in Mie prefecture in Japan, Georgia state in the U.S., Goa state in India, and Sao Paulo province in Brazil, etc., and supplies optical fiber and optical fiber cables worldwide.
Huge amounts of data were recorded and managed on paper, which led to more time and manpower for determining the cause of problems when they occurred.
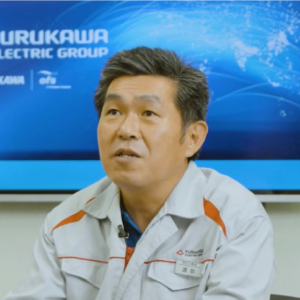
“We value “on-site” above all else in order to build a better product. If there is an accident, the first thing we try to do is to have the right person go to the site to check the situation, then we stop the facility and check the accident carefully.” – Mr. Watanabe.
Furukawa Electric is thoroughly committed to the concept of “on-site, actual, and reality.” Understanding the reality by looking at the actual thing. They do follow-up meetings every day to gather feedback from the work site and check whether there are any abnormalities in equipment or manufacturing management.
All work logs and equipment inspection record sheets were recorded on paper at their optical fiber cable’s production line. These documents were filed by categories, and details were compiled as necessary. “Filing alone used to take 200 minutes every month.” – Mr. Watanabe.
The first step to tabulate the data is to transcribe them to Excel, etc., as most data are handwritten. In addition, since the data to be tabulated is different depending on the contents to be analyzed, the company felt transcribing and tabulating the necessary details each time was time-consuming.
“It takes a long time from filing to searching. We also required an enormous amount of space to save all these papers. The work site has given us a request to do its best to reduce paper.” – Mr. Watanabe.
Approximately 15,000 sheets of paper were used annually for form storage, and an enormous storage space was required. Plus, one of the biggest challenges was when quality problems occurred.
If a problem arises, the cause must be clarified. When collecting details from past manufacturing histories and verifying whether there were any problems in the manufacturing process, the company organized the details by finding the relevant data in the filed paper documents, tabulating them in Excel, and making them into graphs.
Since the documents are managed on-site, they physically move the forms from one location to another and find the right ones. The time they spent during this process was quite long. It took several days for several team members to organize the details, set up a meeting to analyze it, and determine the cause.
“We have a quality problem, but we can’t take action for several days. The inefficiency of this part of the business process was the issue we most wanted to resolve.” – Mr. Watanabe.
At the same time, the company decided to start improving its business process by becoming a smart factory utilizing IoT. The entire department had “what we want to become” in their minds.
“Manufacturing that predicts the quality of the facility, materials, and products, and automatically adjusts the conditions.”
One of their goals comes from the word “predict.” In a future where we must foresee various things, achieving this goal won’t be easy if we spend time on paper as it has been done in the past. For Furukawa Electric, one of the ways to get closer to “what we want to become” was to become paperless by doing the management procedures digitally.
“What should be digitized?”
Why Furukawa Electric choose “on-site” for this.
To work on the “paper to digital” initiative, Furukawa Electric created a project team of about eight members.
The first step they took was examining “What is the best way to acquire manufacturing data?”
Will the company use a form software to digitize records from the production line, or will they continue to take records on paper at that line, scan the words on the paper, convert them to data, and create a database? At this time, when digitization was becoming a trend, the company had many options to digitize, and these two remained the final options.
After visiting the IoT solution’s exhibitions and discussing with the team, they finally decided to “digitize the records that came from on-site.”
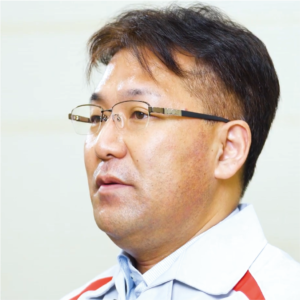
“It was important for us to be able to quickly absorb the necessary details at the right time. When handwritten details are digitized, some kind of conversion process must be adopted.
If we were going to digitize, we also wanted to centralize all details.” – Mr. Matsumura.
Changing the on-site procedures takes a lot of courage and may seem time-consuming. However, the company felt that digitizing the details coming from employees, who are the key to manufacturing and ones that are facing the equipment and products, would lead to better work efficiency in terms of collection and management.
Furukawa Electric learned about i-Reporter at an exhibition, and the deciding factor in adopting it was also “on-site.” The first criterion for selecting i-Reporter was “whether the on-site members can easily use it.”
“I liked the fact that we could simply convert the details of the form we have been using in the past directly to iPad, rather than having to write a new form. Even if the input work is replaced by a form software, we can complete the task at the same speed, possibly faster. That’s what was important to us.” – Mr. Matsumura.
While there are differences between paper and iPad, the templates are similar to the forms previously used, so the burden for changing tools will be reduced at the site. The company felt that as long as they got used to the task, they could enter the data more quickly than before. Also, they felt that an iPad would be easier to carry and manage compared to paper.
In addition to usability, the company was also looking beyond “paper to digital” to “digitizing the facility data” and using various details to support the work on-site, as these were also the deciding factors in deploying i-Reporter.
Use i-Reporter effectively with generous support.
The goal is to get everyone to use the software, not just a few members.
Although the emphasis was on “whether the on-site members can easily use it,” Mr. Uehara recalls that the company needed to take an ongoing approach to change the way things were done in the past.
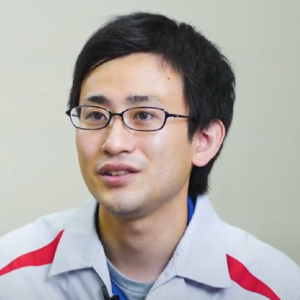
“After we started using i-Reporter, we attended the workshop hosted by CIMTOPS, and it has helped us a lot. Six out of eight project members have participated and learned the basics of the software. You might know what to do after attending these kinds of workshops, but it is much different when you actually use it. We were afraid of making mistakes, and it was difficult for us to deploy i-Reporter to the production line.”
What helped the company was the “Basics of i-Reporter” video provided by CIMTOPS. Whenever they felt unsure or lost, they watched the video two or three times to learn how to use the software.
In addition, when replacing their own quality record forms with templates for iPad, CIMTOPS introduced them to an agency that will directly come to the office located in Mie prefecture to help work with them on creating templates. Members explained that the key to using this software was getting support offline and looking at the same screen together rather than getting help online.
Project members who have mastered using i-Reporter started deploying i-Reporter to the production line by providing OJT one hour a day for about two weeks.
At the same time, the company held a briefing session for employees who will use i-Reporter at the production site, explaining the improvement of tasks and the vision and purpose of digitizing data. Why are we moving quality records from paper to form software? The company wanted to make sure everyone could get the right message about what they are trying to achieve in the future, not just improving the work efficiency with i-Reporter. In addition, once the software was ready to be used at the production site, the company asked everyone to write down concerns (about entering data) every day so the company could try to solve the issue on the same day.
The company felt it was important to know their future goals and share them with members on-site. Also, they decided to continue listening to needs and requests for improvements. The fact that they were able to continuously brush up on their skills with the help of workshops, videos, and support from agencies led the members in the production line to use i-Reporter effectively at a fast speed.
Connecting to members on-site with better quality.
Using the time made by the deploying i-Reporter.
The benefit of using i-Reporter that we have realized the most is the reduction of management costs, such as manpower and time used for searching through a vast amount of paper and transcribing the data from paper to Excel.
Filing, which used to take 200 minutes per month, has been reduced to 0 minutes by becoming digital. Searching used to take 20 minutes per form, but now it takes less than five minutes. Doing the tasks digitally led the company to eliminate the need for space that was previously used to store 15,000 forms per year.
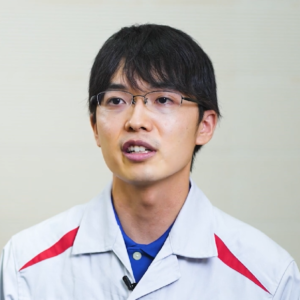
“I have the feeling that finding the data which used to take several days, has become more faster and less time-consuming. After using i-Reporter, I also felt that doing everything analog was a waste of time. The time created by deploying i-Reporter can be used to analyze and visualize data, which could help us lead to the next action.” – Mr. Takeuchi.
The company can quickly retrieve the necessary details from the collected data, convert them into a visual format, and analyze them. They will improve the quality of feedback and improvement, so they can see the “on-site” with better quality. Lastly, they will continue to work with members on-site to promote digitization to improve the on-site work and products.
*This interview is also available by video.
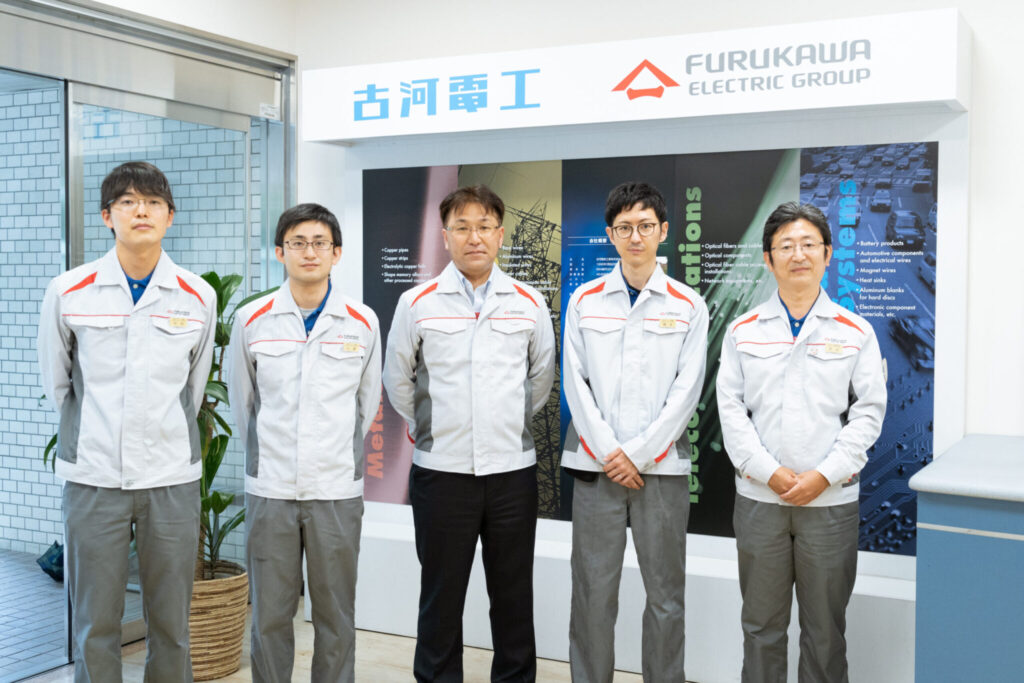
Corporate Profile
Furukawa Electric Co., Ltd.
Companies in various industries and sizes have deployed
i-Reporter in their businesses.
Ranked the number 1 paperless form solution in Japan by marketshare!
-
-
Use your existing paper forms or Excel forms as electronic forms on the go.
The best digital form solution for your business.