Customer Stories: Toyota Motor East Japan, Inc.
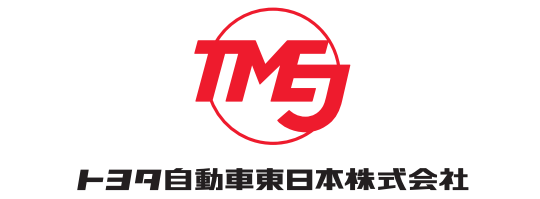
Toyota Motor East Japan, Inc.
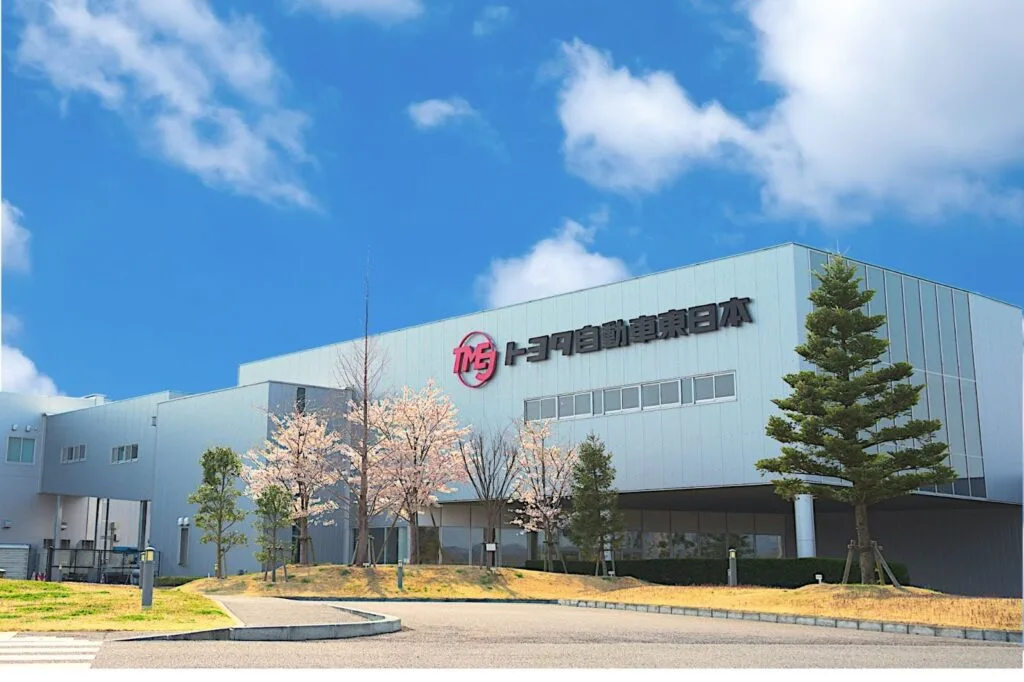
Improvement in product quality and reliability by integrating
i-Reporter with external systems
How the work style has changed
-
Lots of work after creating the report on paper. (e.g., copying the details into Excel to create a daily report, graphing each KPI from scratch, etc.)
-
After the maintenance, the number of failures, analysis reports, and the progress of countermeasures are automatically updated and can be checked easily.
-
Difficult to grasp the current situation and progress of the manufacturing site.
-
The important details can be checked on time, leading to no preparation work for creating the report.
-
Many hours are required to draft the inspection results for several hundred parts in one car model and create a graph afterward.
-
Integration with the digital torque wrench led to automating the process of torque entry, daily calculations, and trend analysis.
-
Information System Department DX Promotion Team Yusuke Goto
-
Iwate Plant Manufacturing Department Jun Yoshida
-
Iwate Plant Manufacturing Department Shinya Sato
From Tohoku to the world. The world-class manufacturing plant for compact cars.
Mr. Goto: Toyota Motor East Japan, Inc. was founded in July 2012 by merging with Kanto Auto Works, Central Motors, and Toyota Motors Tohoku to become a world-class manufacturing plant for compact cars. Throughout the process of planning, development, and production, we make our best efforts to achieve our mission, “From Tohoku Region to the World, provide attractive compact car to customers speedier.”
We have five bases in Japan and two bases overseas. The Head Office, Miyagi Ohira Plant, and Iwate Plant produce cars. Miyagi Taiwa Plant produces auto parts such as engines. Higashi Fuji Integration Center mainly works in the development of cars.
The main factor in deploying i-Reporter was when CIMTOPS provided us with the database.
Mr. Goto: After we looked at many products at the exhibition, we decided to deploy i-Reporter because we can start small. First, we tested with 5 users. Right now, 280 users are using i-Reporter, and we are running about five servers.
Another deciding factor was that CIMTOPS provided us with the i-Reporter’s database and specifications. We found out that not only can i-Reporter create electronic forms and integrate them with BI tools but also integrate with data in our internal tools, allowing us to do secondary processing.
If i-Reporter was only a system to create electronic forms and save them on the cloud, we wouldn’t have deployed it.
The first thing we tried with i-Reporter was digitizing maintenance reports.
Before, we had to create reports on paper, copy the details into Excel, and graph each KPI from scratch. It took a lot of hours to do these tasks.
Also, getting the latest updates on time was difficult.
Now, we enter the details in i-Reporter after the maintenance. Based on this report, we use a system called Motionboard to check the number of failures, analysis reports, and the progress of countermeasures.
Now that we can check the details we want to know on time, we no longer have to prepare materials for meetings, which allows us to save a lot of time.
【Improvement example at manufacturing site】
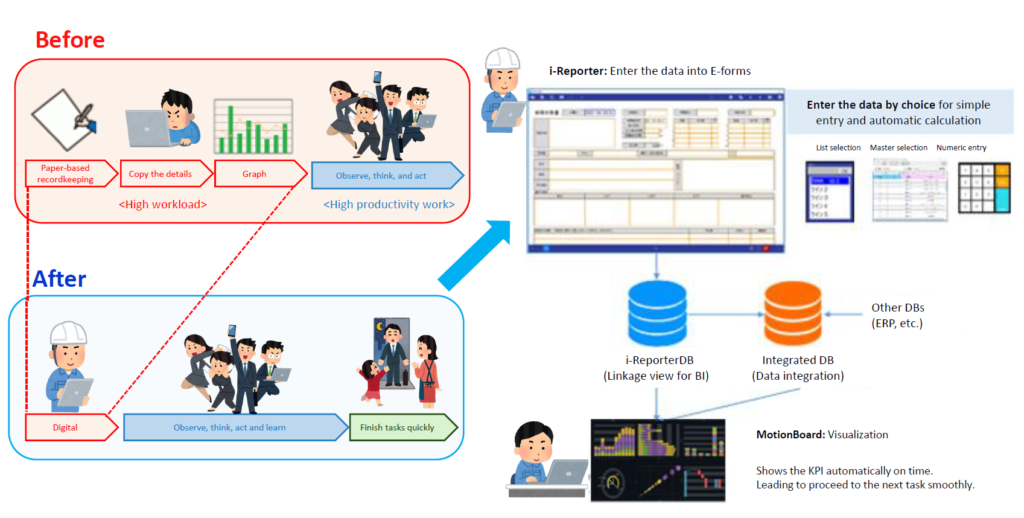
i-Reporter also led to an improvement in product quality and reliability
Mr. Goto: Now that our reports have become digital, the display of various KPIs has been automated. Also, introducing our case study led to a spread to make the tasks digital for other departments and operations.
Among them, the deployment of i-Reporter has helped us with the “X-bar R chart ,” which is our management report for the screw tightening torque.
Mr. Yoshida: The X-bar R chart is a tool for quality control and is used in assembly operations to check if the torque values are stable for fastening parts. There are hundreds of parts in each car, and the “average (X bar)” and “range (R)” are calculated everyday to create one report per part.
Mr. Sato: After the calculation is completed, we plot a line graph to check for exceedances over the threshold, upward and downward trends, abnormality in continuity, etc. Before using i-Reporter, a lot of work by hand was required, especially plotting and drawing lines on paper. Since this work was done after the assembly operations were completed, many employees were working a lot of overtime, which caused a lot of burden on the manufacturing plant.
【X-bar R chart for screw tightening torque】
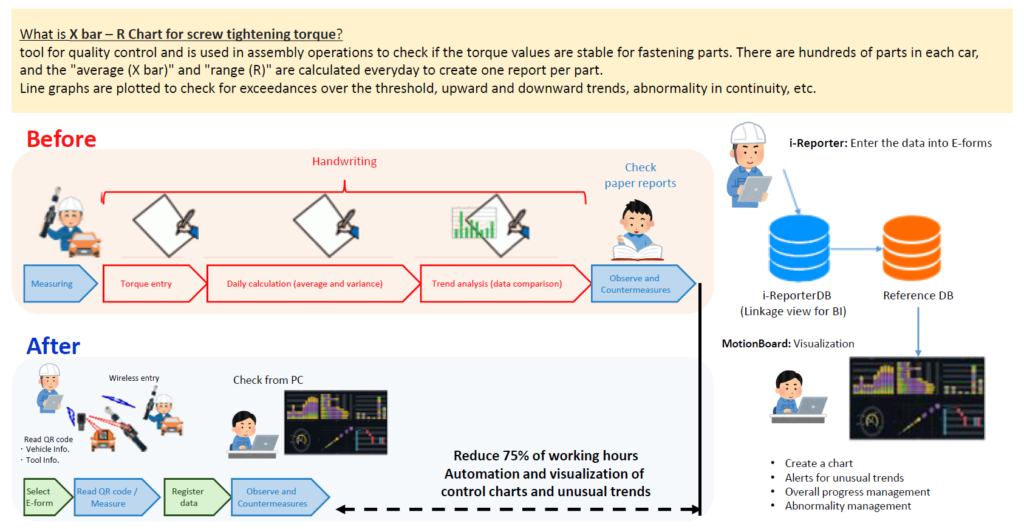
Now that i-Reporter has been deployed, the data can be transferred to the iPad when we press the button on the digital torque wrench, allowing us to transfer the measured data wirelessly. With this, the entire process of torque entry, daily calculation, and trend analysis are now automated.
By deploying i-Reporter, we were able to shorten the working hours and eliminate human errors caused by handwritten data. For the added value, we have added a feature that allows us to compare the data, such as “car details, used digital torque wrench, and measured torque,” with our master data. In the end, this feature led to an improvement in product reliability.
【X-bar R chart for screw tightening torque】
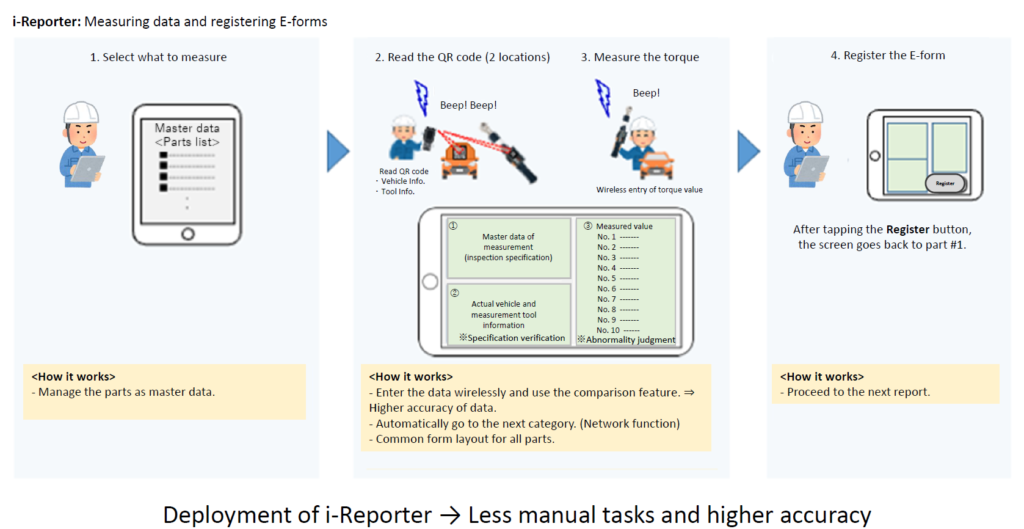
Also, by using i-Reporter’s Network feature, we can automatically control the data entry order and move the cursor to the next category when the entry is completed. This convenience is very attractive for the manufacturing plant’s side. A quick click of the torque wrench automatically moves the cursor to the next category, so there is no need to switch cursors. Like this, we integrate i-Reporter with external systems and hardware to expand the range of usage.
#Software that can be integrated with i-Reporter
#Hardware that can be integrated with i-Reporter
The manufacturing plant requests to use i-Reporter
Mr. Goto: We started to use i-Reporter from a simple check sheet, which is called a work form, but recently, our employees have started to realize that i-Reporter could be used in many other situations.
At first, the Information System Department introduced i-Reporter to the manufacturing plant, but right now, the plant side commonly asks, “Can we use i-Reporter in this situation?”
The Information System Department suggests, “Maybe you can use this tool.” However, many employees want to use i-Reporter because data entry is smoother and easier.
Mr. Sato: When we move from manual to digital, there may be some confusion in the beginning, especially from the older generation that has worked in their career without really using tablets and computers.
But at our company, shifting to digital has significantly impacted the employees’ personal lives, as those in their 60s who have been using i-Reporter at work say things like, “I think I should start using an iPhone.”
Mr. Goto: “From Tohoku Region to the World, provide attractive compact car to customers speedier” is our mission.
We will continue to use digital technologies such as i-Reporter and aim to become a “Smart Factory” that delivers better products to our customers worldwide.
Corporate Profile
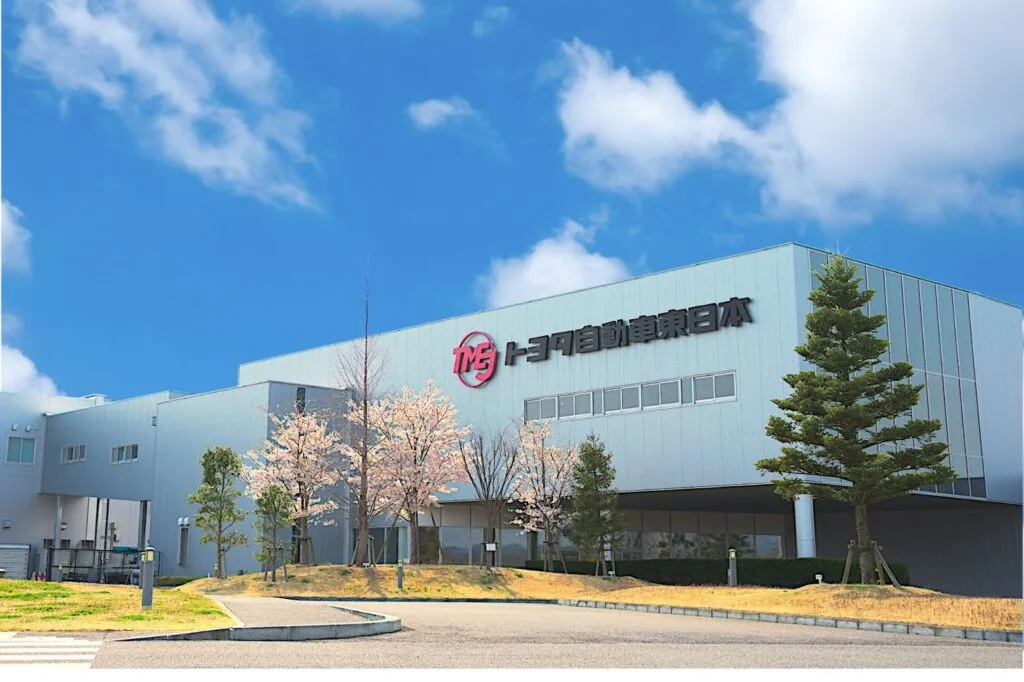
Toyota Motor East Japan, Inc.
- Founded in:
- July 2012
- Head office:
- 1, Chuo-daira, Ohira-mura, Kurokawa-gun, Miyagi Prefecture
- Business activities:
- Planning, R&D, production of Toyota cars
Companies in various industries and sizes have deployed
i-Reporter in their businesses.
Ranked the number 1 paperless form solution in Japan by marketshare!
-
-
Use your existing paper forms or Excel forms as electronic forms on the go.
The best digital form solution for your business.