Customer Stories: Kureha (Changshu)Fluoropolymers Co.,Ltd,
Kureha (Changshu)Fluoropolymers Co.,Ltd,
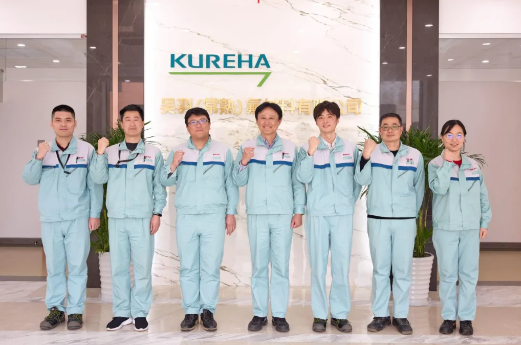
i-Reporter use case and case study: Kureha (Changshu)Fluoropolymers Co.,Ltd.
Challenges faced before implementation
- Reducing the burden and errors associated with paper-based forms and manual data entry into Excel at the work site.
- Promoting digitalization of operation procedures and checklists that were previously recorded on paper, without causing any disruption to the site.
- Operation to efficiently utilize the information obtained at the site to achieve rapid issue resolution and drive new innovations.
Reasons for adopting mcframe RAKU-PAD, an OEM product of i-Reporter
- Create input form on PCs and tablets almost directly from Excel and paper forms (Recording function).
- QC7 tools such as control charts and Pareto charts necessary for quality control and production control are available (Analysis Dashboard function).
- Seamless sharing, aggregation, and analysis of input data.
Results post implementation
- Eliminating the need for transcribing from paper and utilizing automated data entry in some cases has achieved efficiency and reduced errors.
- As a model case, departments that have embraced the system have strengthened collaboration and information sharing among departments.
- The inputted data, such as lot numbers and personnel names, is automatically saved and calculated, ensuring data continuity and enhancing data reliability.
- By eliminating transcriptions, accurate data can be instantly shared among stakeholders.
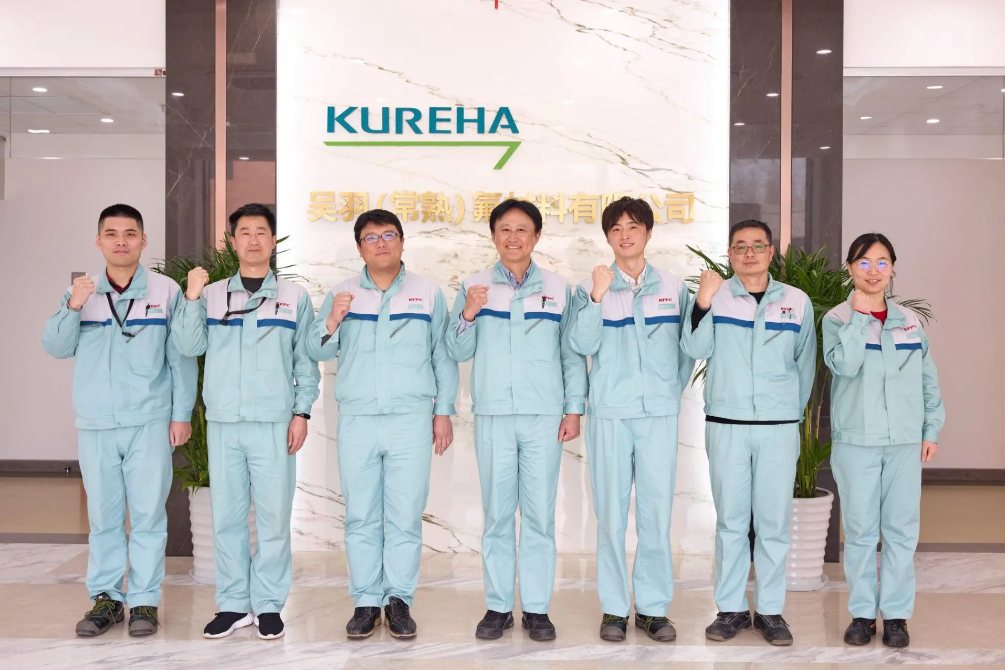
Kureha (Changshu)Fluoropolymers Co.,Ltd,
A production site of the Kureha Group, specializes in manufacturing high-performance fluororesins, with a focus on vinylidene fluoride resins used in materials for lithium-ion batteries. The company faced challenges in areas not covered by the the plant control system, where paper-based records were prevalent. This resulted in issues regarding data accuracy and freshness, making it difficult to effectively utilize the data. To address these challenges, the company introduced the data recording, analysis, and utilization tool “mcframe RAKU-PAD” (hereinafter referred to as RAKU-PAD) from Business Engineering (B-EN-G) in 2021. Some departments have adopted advanced practices, such as automated input of personnel names and lot numbers using QR codes and interface integration with electronic balances, promoting the development of smart factories driven by the efforts of the operation site.
Kureha (Changshu)Fluoropolymers Co.,Ltd,
Website: http://www.kureha-kfpc.com.cn/jp/
Established: 2012
Number of Employees: 117
Business: Vinylidene Fluoride Resins
Located in Changshu Advanced Materials Industrial Park, Jiangsu Province, China, Kureha (Kureha Fluoropolymers Co.,Ltd, was established as a production base of the Kureha Group with a registered capital of 60 million USD, thanks to investments from Kureha (China) Investment Co., Ltd. The Phase 1 project, which was officially completed in April 2014, has an annual production capacity of 5,000 tons of Polyvinylidene Difluoride (PVDF) and is currently considering expansion plans for a new plant due to increasing demand.
The remaining paper-based tasks within our China factory facility, which plays a crucial role in our global supply chain, are a challenge we are facing.
KFPC (Kureha(Changshu)Fluoropolymers Co.,Ltd,), which produces Polyvinylidene Difluoride (PVDF), a type of fluororesin, was established in 2012 as a PVDF production site within the Kureha Group’s global supply chain in China. During the establishment of KFPC, the company adopted the management practices from Kureha’s PVDF production site in Iwaki City, Fukushima Prefecture, Japan, as the mother factory. However, over time, they began to identify areas for improvement, as explained by Mr. Saito.
“While important aspects of plant control are handled by DCS (Distributed Control System), there were many instances where various data and information were recorded on paper. Additionally, digitizing work procedures and checklists proved to be challenging. The process of transferring this paper-based data into Excel was a significant burden,” – Mr. Saito.
The decision to introduce mcframe RAKU-PAD was made considering its compatibility with on-site operations and workflows.
First, KFPC started the initiative to digitize paper records on the site. Mr. Ohira, the Manager of the Project Promotion Department, explains the reason for selecting a digitalization tool for paper documents as follows:
“As part of our efforts to improve business efficiency, we decided to digitize paper-based processes. We consulted with Hamasho Corporation(SUZHOU)Ltd., a machinery trading company with whom we have had previous dealings and which also handles B-EN-G’s IoT solution sales. They introduced us to RAKU-PAD. We felt that it had compatibility with the plant operators’ tasks, so we decided to give it a try.” – Mr. Ohira
RAKU-PAD allows creating input form on PCs or tablet devices that closely resemble the format of Excel sheets or paper documents. Additionally, it enables seamless data sharing, aggregation, and analysis, leading to a wide range of potential applications.
“We not only aimed to enhance input efficiency with RAKU-PAD’s Recording function but also wanted to create an environment where even non-IT departments could easily conduct trend analysis for quality management in manufacturing. That’s why we also adopted RAKU-PAD’s Analysis Dashboard, which includes essential QC 7 tools such as Control charts and Pareto charts.” – Mr. Ohira
By utilizing automated inputs, we effectively reduced manual efforts and minimized errors, ensuring data continuity.
In the Quality Management Department, where RAKU-PAD utilization is most advanced, they conduct product analysis by lots and input the results into RAKU-PAD. They also utilize functions to automatically determine pass/fail results as needed. Mr.Kasuya explains that the implementation of RAKU-PAD has resulted in reduced effort and concerns about input errors when transferring data to Excel. They are actively utilizing RAKU-PAD for various purposes, such as automatic inputs using QR codes for personnel names and lot numbers, as well as automatic inputs from electronically connected scales.
The reduction in effort and errors in these tasks was achieved through ingenious measures within the Quality Management Department, as shared by Mr.Yin.
“At the initial stage of RAKU-PAD implementation, we used to input lot numbers and other data manually through the keyboard. However, when we discovered that QR codes could be used for input, we gradually transitioned and started creating seals for this purpose. Thanks to this change, we eliminated mistakes in data entry, and once the input is done, RAKU-PAD automatically saves and calculates the data, ensuring data continuity,” explains Mr. Yin.
RAKU-PAD’s utilization has gone beyond merely reducing data entry tasks. It has led to the digitalization of approximately 75% of the total report types in the Quality Management Department, resulting in significant business efficiency improvements and a shift towards paperless operations. The implementation of RAKU-PAD at the site involved collaborative efforts with B-EN-G Shanghai, where trial and error were essential parts of the process.
“We are highly satisfied with the dedicated support provided by B-EN-G Shanghai, including training for creating reports and assistance in developing specific report formats. B-EN-G Shanghai has been proactive not only in operational support but also in product maintenance. Whenever there have been issues, they promptly address them through subsequent version updates, which has been extremely helpful to us.” – Mr.Kasuya
The utilization of RAKU-PAD in the Quality Management Department has positioned it as a model case for expanding its usage to other departments within KFPC. Particularly, the Production Department and the Equipment Management Department, which work in the plant, are actively seeking to accelerate its implementation. Mr. Huang explains their vision as follows:
“Our plant is designated as an explosion-proof area, so the devices we use must be explosion-proof models. Moreover, online usage is essential within the plant. Due to these factors, the usage of RAKU-PAD in the Quality Management Department, which is a non-explosion-proof area, has progressed well. However, we have faced challenges in meeting the real-time data integration needs of the Manufacturing Department and the Equipment Management Department, which mainly operate in explosion-proof areas. Until now, RAKU-PAD was only compatible with iOS and Windows OS, limiting our options. However, I have heard that it is now possible to input data through some web browsers, allowing us to choose affordable tablets compatible with Android OS and explosion-proof requirements. Once these device and network issues are resolved and RAKU-PAD becomes accessible, we anticipate that we can digitize various reports, such as those informing the Equipment Management Department about equipment malfunctions identified on-site. This will lead to smoother operations, and we have high expectations for these developments.” – Mr. Huang
At KFPC, the plan is to utilize the data obtained through RAKU-PAD as a means for fostering new innovations.
“At KFPC, we are pursuing a strategy known as ‘KFPC Version 2.0,’ aiming to drive reforms towards realizing Smart Factories and Smart Offices. Our first step is to establish an environment capable of storing data effectively, and then leverage this data extensively to foster new innovations.” – Mr. Saito
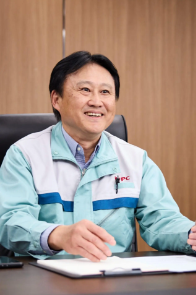
Kureha (Changshu) Fluoromaterials Co., Ltd.
Mr. Futoshi SAITO / Chairman President

Kureha (Changshu) Fluoromaterials Co., Ltd.
Mr. Tsuyoshi OHIRA / Project Promotion Department Manager
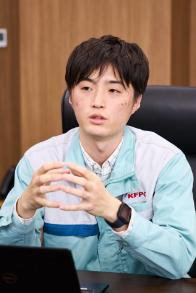
Kureha (Changshu) Fluoromaterials Co., Ltd.
Mr. Yuki KASUYA / Process Engineer
For the implementation of i-Reporter at Kureha Changshu, we received strong support from Mr. Zhao Liwei (a consultant who is also proficient in Japanese) at Toyo Business Engineering (Shanghai) Co., Ltd. They provide comprehensive support ranging from requirement confirmation tailored to customer operations to configuration, training, and maintenance.
We had the opportunity to learn about the features of their technical support from Mr. Kodama, Deputy General Manager at Toyo Business Engineering (Shanghai) Co., Ltd.
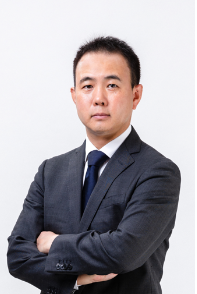
Toyo Business Engineering (Shanghai) Co., Ltd.
Deputy General Manager
Mr. Junya Kodama
Our experienced consultants with a wealth of experience in system implementation for manufacturing industries will provide support tailored to your business needs, ensuring an easy-to-use system. Rather than simply digitizing Excel reports, we aim to create a user-friendly system with simplified input forms and output capabilities similar to your current processes.
As a System Integrator, we are not just a mere agent but take full responsibility for the system implementation with our in-house IT consultants, ensuring a seamless process without outsourcing to other companies.
Our analysis feature (mcframe RAKU-PAD Analysis Dashboard) is exclusively developed for i-Reporter, enabling easy integration with just a single button. We have equipped standard tools such as control charts and Pareto charts, covering QC Seven Basic Tools.
From i-Reporter to MES and ERP system implementations, we can provide a comprehensive range of IT systems necessary for manufacturing sites, offering consistent support throughout the entire process.
Business Engineering Corporation has been an authorized distributor of i-Reporter, providing support for i-Reporter implementation globally in countries including China, Singapore, Thailand, Indonesia, Malaysia, the Philippines, the United States, Canada, and Mexico.
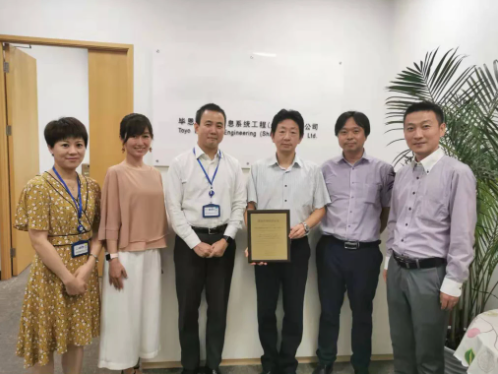
B-EN-G Shanghai – Sales Consultant, Sales Division/ Ms. Wan Yan
CIMTOPS – Sayaka Oide
B-EN-G Shanghai – Deputy General Manager/ Mr. Junya Kodama
B-EN-G Shanghai – General Manager/ Mr.Sun Qiang
CIMTOPS – Li Changlin
CIMTOPS – Lu Yonghu
Corporate Profile
Kureha (Changshu)Fluoropolymers Co.,Ltd,
Companies in various industries and sizes have deployed
i-Reporter in their businesses.
Ranked the number 1 paperless form solution in Japan by marketshare!
-
-
Use your existing paper forms or Excel forms as electronic forms on the go.
The best digital form solution for your business.