Customer Stories: SEKISUI SEIKEI Co., Ltd.
SEKISUI SEIKEI Co., Ltd.
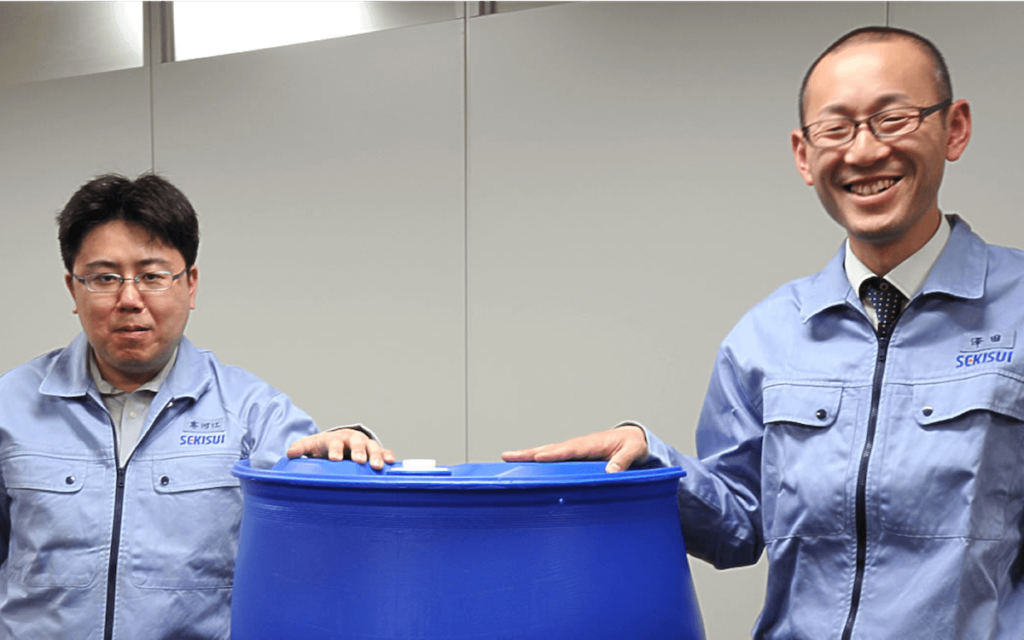
i-Reporter use case and case study: SEKISUI SEIKEI Co., Ltd.
SEKISUI SEIKEI Co., Ltd.
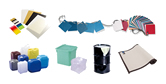
SEKISUI SEIKEI Co., Ltd makes daily manufacturing electronically available with using i-Reporter
Sekisuii Seikei uses i-Reporter for creating daily reports, counting, data transfer, and administration. Previously, manufacturing daily report was made by paper and on Excel, but to improve work efficiency, it was computerized.
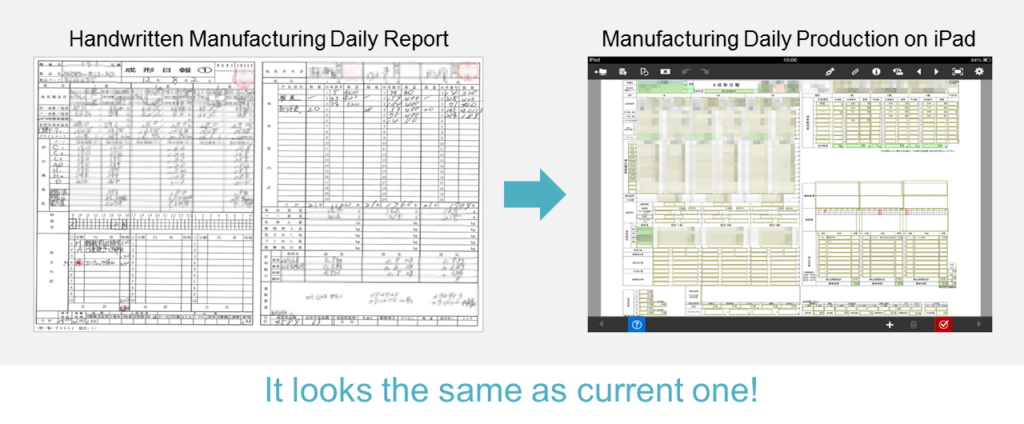
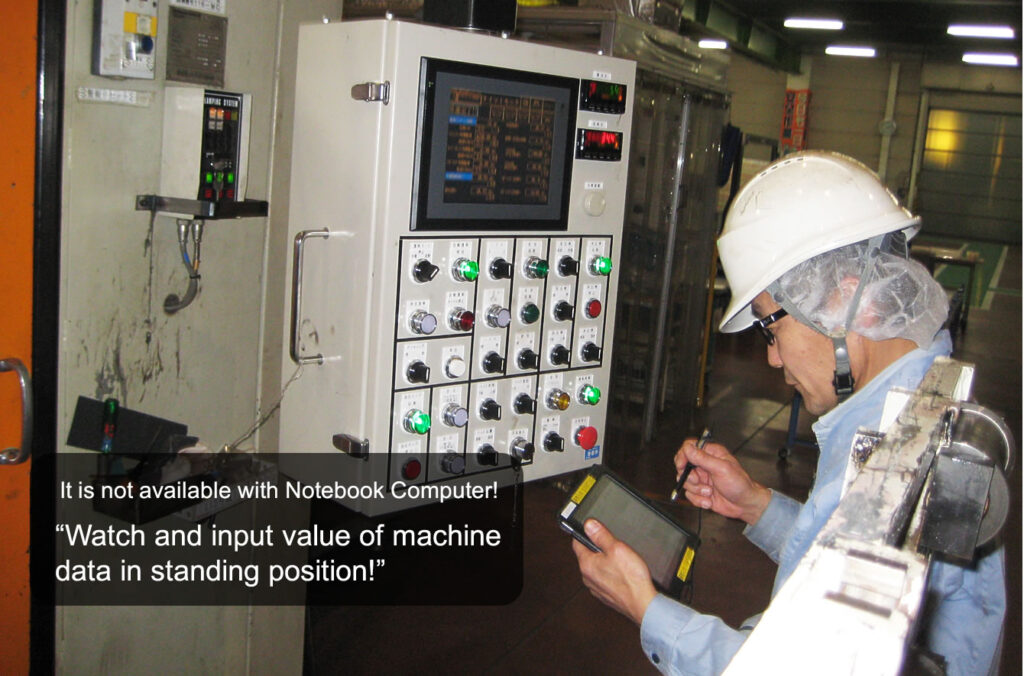
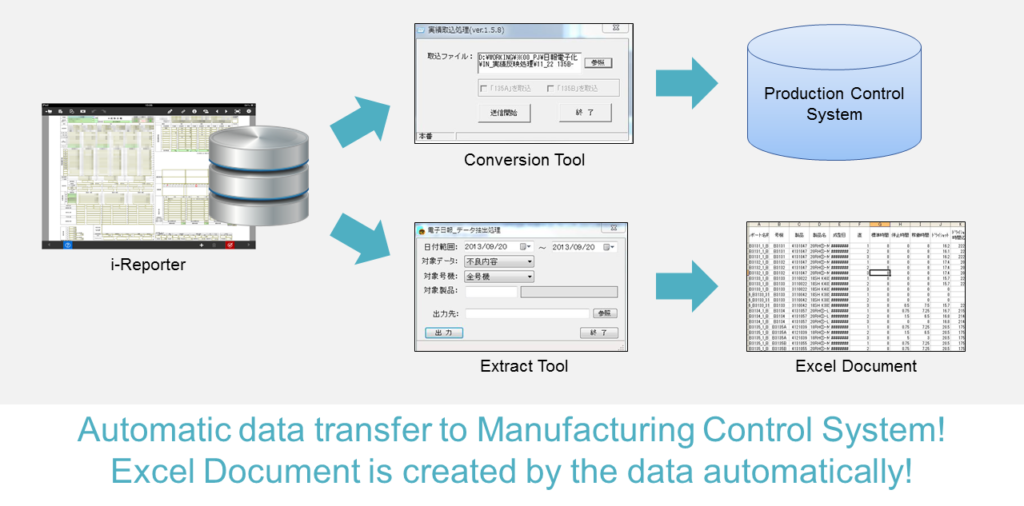
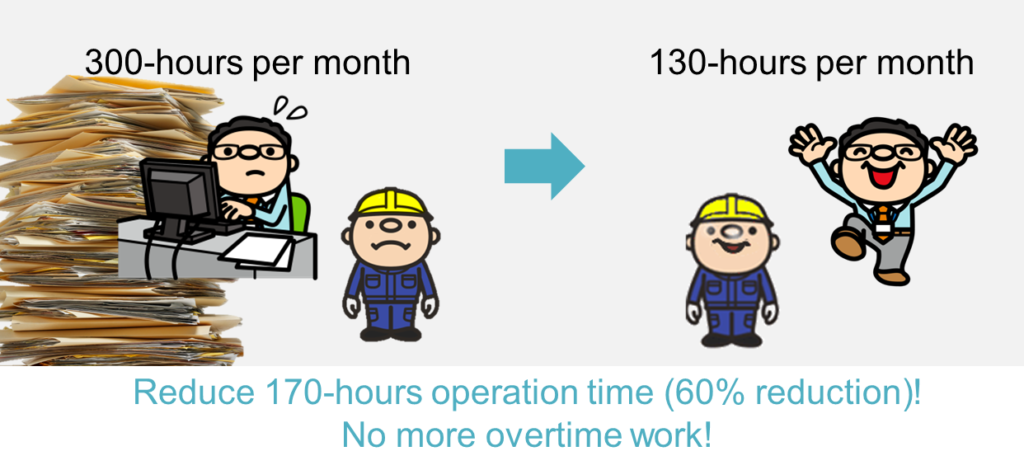
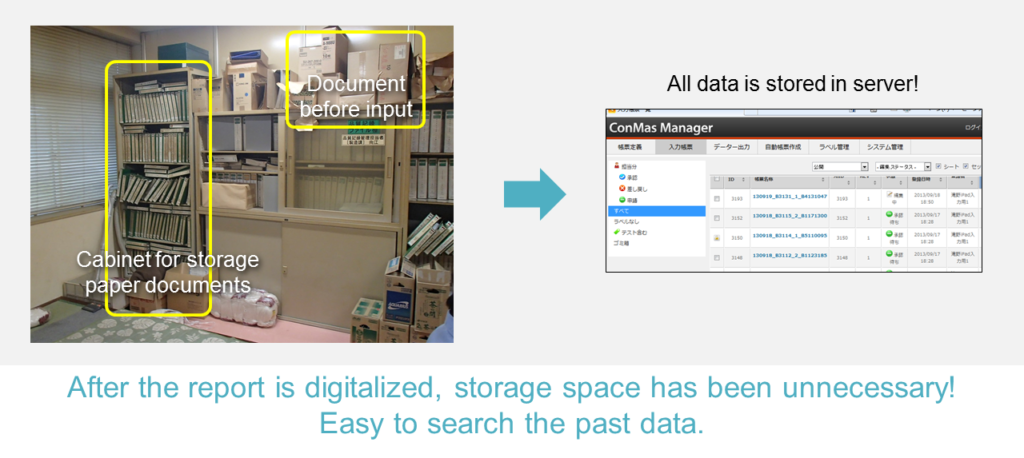
Introduction Effects
iSekisuii Seikei started using i-Reporter at Takino Factory. Here is the summary:
Items | Previous status (Using paper and Excel) | → | Managed by i-Reporter |
---|---|---|---|
Data transfer errors | Frequently occurred. Handwriting is sometimes difficult to read. Transcription errors often occurred. 0 and 9 or 1 and 7 were often confused. | → | No error form transcription errors with i-Reporter. |
Counting | We previously counted by hand. Some cases required complicated calculation, therefore, going over the accounts to verify was also complicated. | → | i-Reporter does automatic calculation for us. (No more calculation errors) |
The Human Burden | The night shift staff stayed overtime and worked until 8:30AM to compile the daily report. | → | Auto excel file creation by i-Reporter. (No more overtime work to make the daily reports) |
Overtime | Daily overtime was required to finish the daily report. | → | No more overtime for making the daily reports. |
Production schedule | Every morning, we had to write the schedule regarding production items based on the instruction sheets from the production control system. | → | The data is directly extracted from the i-Reader database. |
Entering actual performance into the production administration system | Deep knowledge and a staff well trained in our own internal coding nomenclature were required. The staff entered their own code based on the handwritten daily reports. Average 17 pages/ day x 3 shifts = 51 times. 15 min / page x average 17 pages = 255 minutes (about 4.5 hours). | → | The data is directly extracted from the i-Reader database and transferred into the production control system. |
If the Manger of Manufacturing asked, “May I see other data?” | It took another 90 minutes to transfer the data to Excel. | → | Data is already changed to the Excel version. |
Archiving | Filing and storage in racks. The required a lot of physical space. (Three years files have to be kept for ISO regulation.) | → | Digital Archive |
Search | Fought with a pile of papers and files. | → | Quick search of the database |
Meeting before work | Circulate one piece of paper to ten people (No time to make copies for everyone). | → | Everyone individually checks their own screen. |
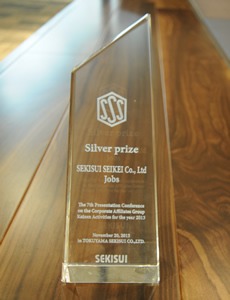
Internally, using the product was highly complimented. We won the Sekisui Chemical Group kaizen contest silver award in 2013. It was first time the Project Information System Department received an award.
Three reasons why daily reports weren’t electronically available until then
– Q: Can you tell us the details why laptop PC is not appropriate at the site?
- A Laptop PC is not appropriate to use while standing
- Manufacturing sites didn’t feel it was necessary
- There was a psychological distance between the manufacturing sites and the Information System department
Reason 1. A Laptop PC is not appropriate to use while standing
– Q: Can you tell us the details why laptop PC is not appropriate at the site?
A: We feel that Laptop PC is not appropriate to use at site essentially because we can not enter the data on note PC while standing, and then Laptop PC is expensive but break down easily. Manufacturing sites are hot and humid. There also is dirt and dust. Laptop PC’s will frequently brake down.
However, these concerns are solved after a tablet such as the iPad shows up.
First of all, information on the tablet can be entered while standing. Also, the price is more reasonable than for a laptop PC.
The tablet made it possible to make the daily reports electronically available.
Reason 2. Manufacturing sites didn’t feel it was necessary
– Q: Can you tell us the details why manufacturing sites didn’t feel it was necessary?
A: For many years, they had been making daily reports by paper and Excel. Nobody questioned it. Overtime work was required. But if you think, “it is like that”, then it is okay with everyone.
Even if you proposed “digital daily reports”, the reaction you got was “More of a burden”, “Too difficult,” or “Hard to learn how to use it”. Also stated was “The current way is okay,” or “We don’t want to change”.
Reason 3. There was a psychological distance between the manufacturing sites and the Information System department
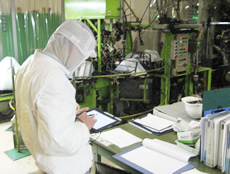
A: Previously, Information System Department and each manufacturing sites didn’t communicate enough. Osaka HQ and Hyogo Takino factory (Hyogo), Kanto factory (Ibaraki), Hyogo factory (Hyogo) and Chiba factory (Chiba) and Izumo factory (Shimane) are physically apart and I personally didn’t have opportunity to meet the employees at the sites.
If you state to the sites, “Digitalization of the daily reports makes the company better”, the manufacturing staff would say, “You don’t know the real site’s situation”, “It’s the grandstanding of the Information System Department”.
To implement daily digital report, psychological resistance was a huge barrier between the Information System Department (HQ) and sites (manufacturing department).
This time, what is the cause to digitalize daily reports?
– Q: You eventually got rid off the obstructive factors. What is the story behind that?
A (Mr. Sawada): One of the biggest factors was the influence of Mr. Sagae from the Hyogo Takino factory. Mr. Sagae and I joined a company at the same time, so we knew each other.
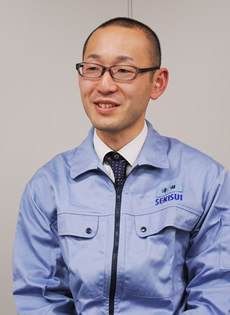
A (Mr. Sagae): My initial motivation was “I want do more efficient personal work (reduction of my working hours)” rather than a lofty motivation, such as “I want to improve the whole factory.”
I was in charge of making manufacturing material and entering production data in to the administration system, and it took me 4 hours and half each day.
One day, I talked to newly posted manufacturing manager, “I think the current situation is very inefficient”, then he said, “That is right, better work on it.”
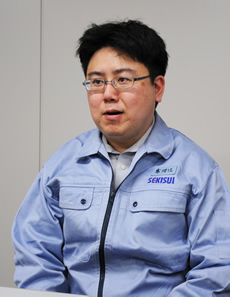
A (Mr. Sawada): Immediately, I started collecting information about daily reports digitalization software. For one of the research activities, I went to an IT exhibition in Tokyo and saw i-Reporter at CIMTOPS booth, with the banner stating “Digitalizing Reports by iPad”. When I heard the details, it sounds like it had everything I wanted.
Selecting software
– Q: What is the next action?
A (Mr. Sawada): We focused on selecting software. Mr. Sagae said, “i-Reporter is pretty good, but there may be some other great products. So we collected other product information. The products for final consideration were i-Reporter and work flow software, which is web-based.
Comparison Criterion
Here again are our requirements. This time specifically comparing the i-Reporter and Workflow products. i-Reporter was superior for all requirements, so we decided to implement it.
The superior points of i-Reporter
Here is the comparison sheet between i-Reporter and other products.
Requirements | i-Reporter | Other Workflow products | |
---|---|---|---|
1 | Usability by tablets | ◎ (The software was designed specifically for the tablet) |
○ (the software was designed for the PC but a tablet could be accommodated) |
2 | Availability off- line | ○ | × (Not possible due to web form) |
3 4 |
Visually the same appearance as the traditional paper version Included in one paper sheet |
○ | × (Not good, looks web formish) |
5 6 |
Easily integrates with the production administration system Easy data extraction |
◎ (CSV Direct access to the database by SQL) |
○ (Only CSV) |
7 | Cost of introduction | ○ (Half the price of Work flow) |
△ |
Key points of smooth i-Reporter introduction to the site
Here is the summary of how we introduced the i-Reporter.
- Explaining the reason behind using the new product
- We paid full attention not to have a condescending and arrogant attitude
- We asked people at the site to be critical while checking the i-Reporter
- Thoroughly responded to support requests and needs
Key point1: Explaining the reason behind using the new product
A (Mr. Sagae): When I explained the plan for changing the way we made the “manufacturing daily reports”, I honestly explained to them, “My working hours are totally consumed by the transcription of the manufacturing daily reports and I have to do overtime to do this work. If we use i-Reporter, overtime would be reduced a lot.” Then, I also explained that digitalization of daily records would make company better overall.
Key point 2: We paid full attention not to have a condescending and arrogant attitude
A (Mr. Sawada): This was a collaboration project with the factory site, which I haven’t done before. Therefore, I wanted to be sure of the product’s success. I didn’t want a negative reaction or misunderstanding because of my attitude. I was sensitive about this.
Key point 3: We asked people at the site to be critical while checking the i-Reporter
A: We politely asked, “From the point of view of working at the site, some things must still not be user friendly. Please feel free to speak out!” It tuned out the staff pointed out a lot of details we didn’t notice and accepted this process, which led to the building up of trust.
Key point 4: Thoroughly responded to support requests and needs
A: For the requests or demands from the site, we did our best to solve it together with CIMTOPS. Here are some details:
Requests from people at site | → | Countermeasures |
---|---|---|
iPads are not easy to hold and may drop | → | A case that fits the hand like a binder was found. |
With cotton work gloves it is hard to write | → | Using the pen made for the tablet which can be held and utilized with gloves. |
Many multiple choices for raw materials but you need to choose only one. This may create errors | → | Hide un-related raw materials |
Before entering data, we want to make sure the master raw material and material from daily reports was correct. | → | A new confirmation screen shows up. |
Even if the molding machines are not operating all day, we keep recording the daily manufacturing reports. | → | Making a code by the digital daily report made it possible to reflect the molding machine schedule. |
Amendment of dry shots to time productivity has to be calculated by hand with calculator. | → | Adjusted items by using auto- calculation. |
Your future expectations
A (Mr. Sagae): We really made the idea of having efficient daily reports at the Hyogo Takino factory come true. We received many compliments from the site and this efficiency made whole factory’s quality go up.
(Mr. Sawada) Through this project, I really felt I could now understand “what the factory site wants” as the person who belongs to the Information System department. I would like to keep suggesting various idea to be useful.
Corporate Profile
SEKISUI SEIKEI Co., Ltd.
Official websiteCompanies in various industries and sizes have deployed
i-Reporter in their businesses.
Ranked the number 1 paperless form solution in Japan by marketshare!
-
-
Use your existing paper forms or Excel forms as electronic forms on the go.
The best digital form solution for your business.